Company Profile
Hangzhou Hanpai Mould Technology Co. Ltd. is Founded in 2012, it’s the Council Member of Zhejiang Die&Mould Industry Association.We specialize in R&D and production of pellet mill machine parts, such as feed pellets ring die, biomass pellets ring die, organic fertilizer pellets ring die, cat litter pellets ring die,roller shell and so on. Provide zero defect pellet mill die for the world is our development goal.
In 2017 year we were honored as the Hangzhou high-tech enterprise and passed the approval of Zhejiang province scientific and technological enterprises. In 2018, the name of our company was changed from Hangzhou Hanpai Mould Co., LTD to Hangzhou Hanpai Mould Technology Co., LTD.We are the Audited Supplier by SGS,now we have got the ISO 9001 quality management system certificate.
Happy Mould use high quality X46Cr13 stainless steel, CNC deep hole drilling machine,vacuum quenching furnace ,other advanced equipment and unique process; At the same time we have a group of high-level technicians and strict production quality control system,which create the Happy Mould excellent quality and good customer reputation.Happy Mould can make efficiency of production Increase 10-40%,cost of production decrease 10-40%
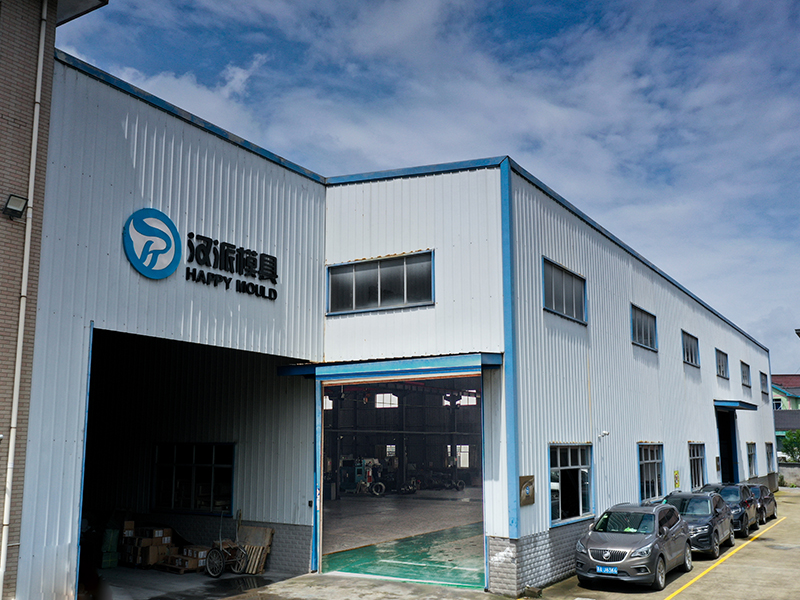
Happy Mould
"HAPPY MOULD" is our trademark, using Happy Mould can make customer save a lot of production costs, increase profits and market competitiveness because of its smooth production, good pellets quality, high production efficiency, low power consumption,and easy operation.It also can reduce workers labor intensity,which bring happiness for everyone.
Hanpai Mould has won wide praise from customers at home and abroad, and we are looking forward to providing excellent and zero defect mould for global pellet production enterprises.
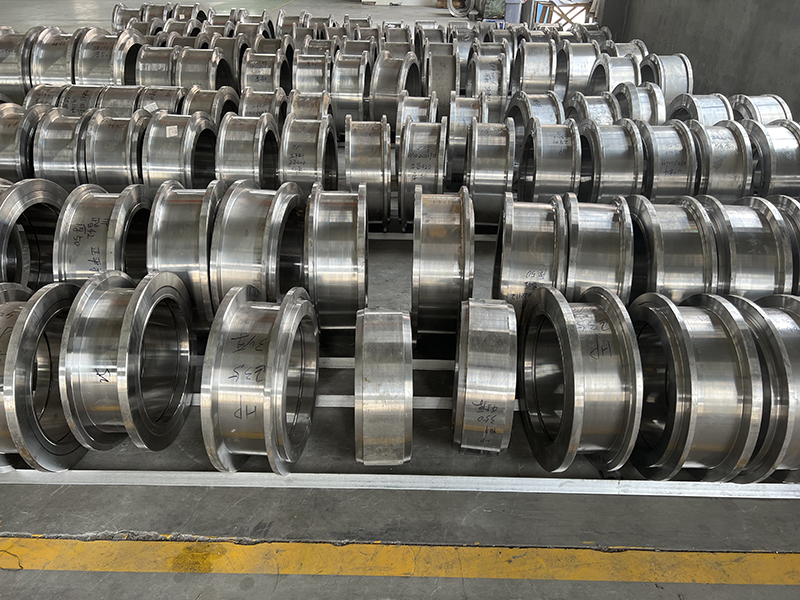
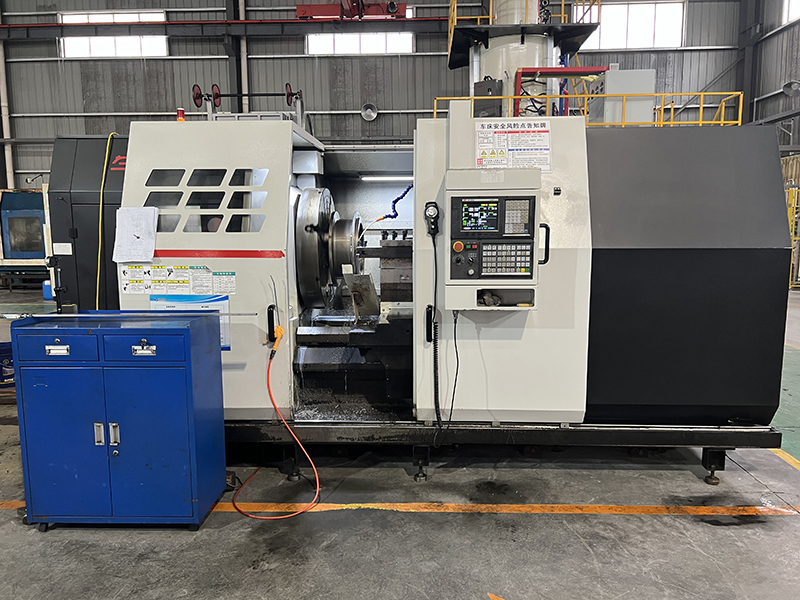
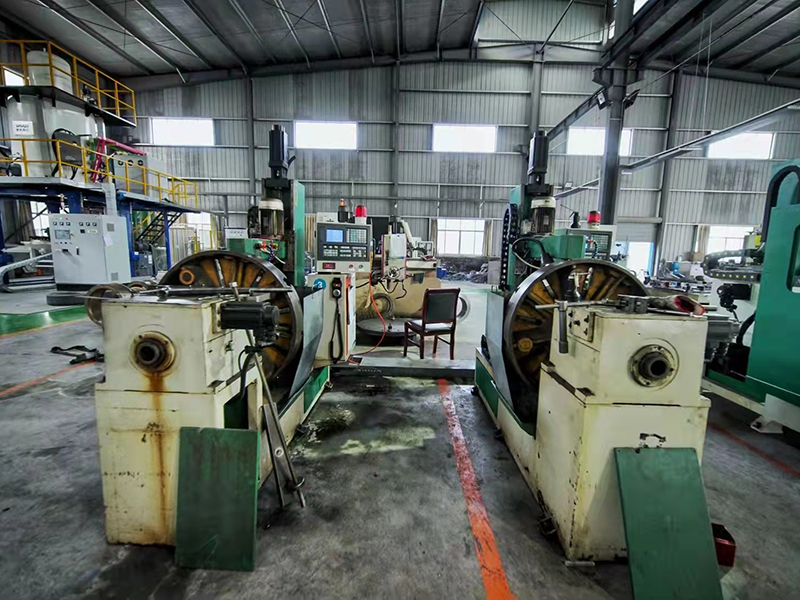
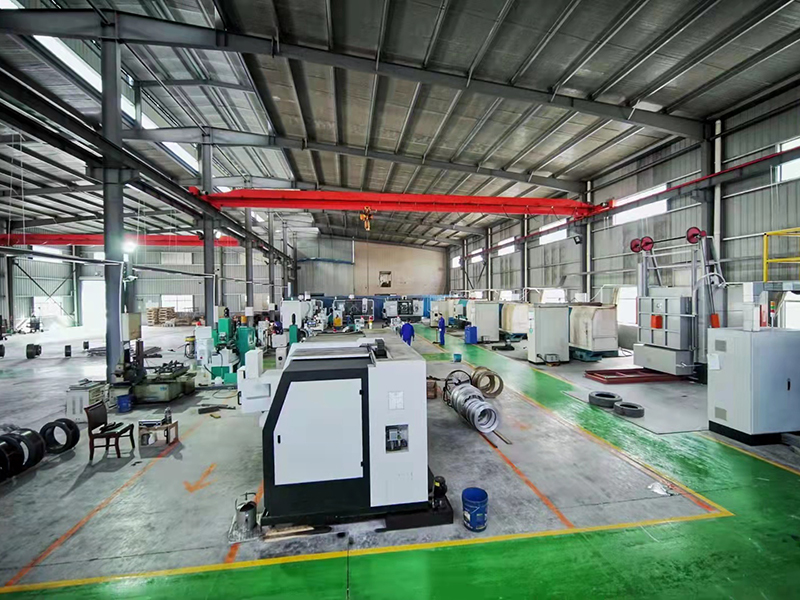
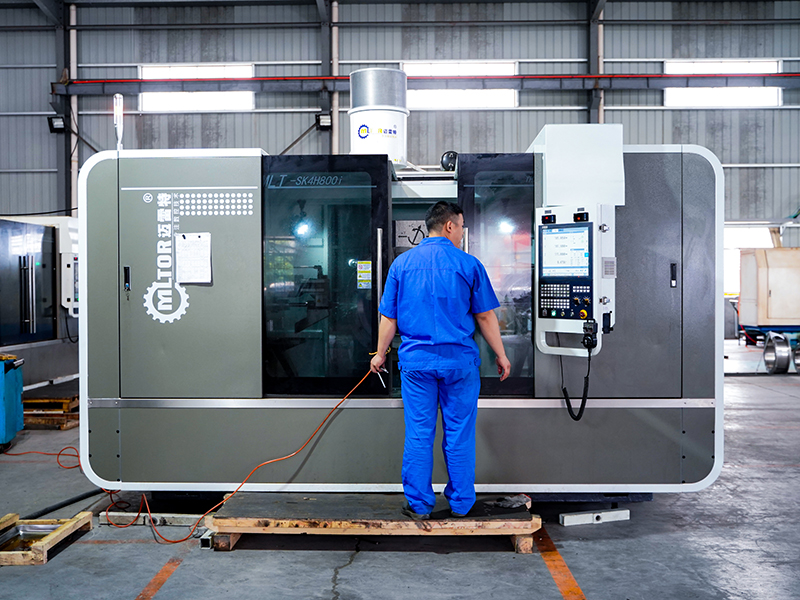
ID in the figure -- inner diameter of ring die;
O -- total width of ring die;
W -- effective width of ring die (working surface width);
d -- aperture of ring die (hole size of pressed pellet);
L -- effective length of die hole;
T -- the total thickness of the ring die;
D -- taper inlet diameter of die hole;
β -- die hole conical inlet Angle;
The hole shape of the pellet mill die: the commonly used hole shapes mainly include straight hole, reverse step hole, outer cone reaming hole and forward transition step hole with cone. Straight hole processing is simple, the most common use; The effective length of the die hole and the material extrusion time in the die hole are reduced by the reverse step hole and the outer taper hole, it is suitable for processing the pellets with the diameter less than φ10mm. The positive reaming step hole with conical shape is suitable for processing pellet feed which the diameter more than φ10mm with high crude fiber content. In addition to the above 4 kinds of hole shapes, there are a variety of hole shapes, such as outer conical hole, inner cone hole and non-circular hole, but the use is not common.
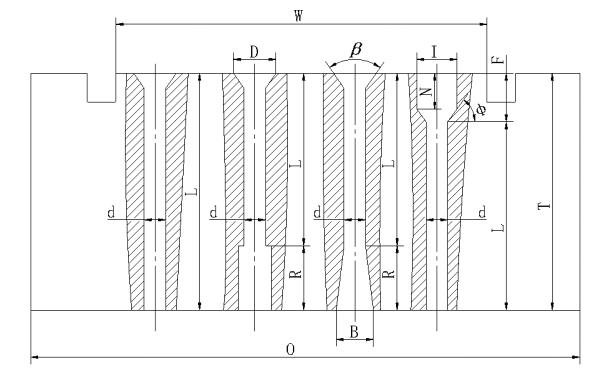
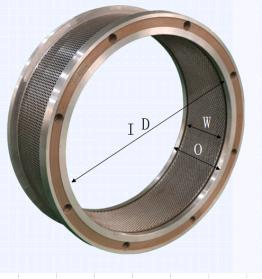
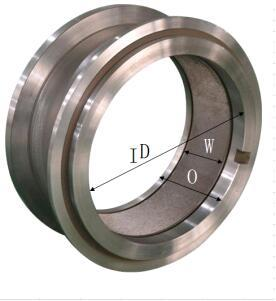
R -- depth of reverse reaming (pressure relief hole);
B -- diameter of reverse reaming (pressure relief hole);
φ -- positive reaming transition Angle;
F -- positive reaming depth;
I -- positive reaming diameter;
L/d -- length-aperture ratio (compression ratio).
Thickness of pellet mill die (T) : The thickness of ring die directly affects the strength,hardness of ring die and the efficiency ,quality of pelleting. In the world, the thickness (T) of the ring die is usually selected from 32~127mm (the minimum thickness in China has been 13mm).
Effective length of pellet mill die hole (L) : The effective length of ring die hole refers to the length of die hole for material extrusion (forming). The longer the effective length of the die hole, the longer the extrusion time of the material in the die hole, the harder the pellets are made, then strength and the pellets quality are better. On the contrary, the pellets are loose, the pulverization rate is high, and the pellet quality is reduced.
Tapered inlet diameter (D) of the die hole: the diameter of the feed hole should be larger than the diameter of the die hole (d), so as to reduce the resistance of the material into the hole, so as to facilitate them entry into the die hole. There are three basic forms of feed holes, namely straight hole, cone hole and curved hole.For raw materials with high fiber content, due to the difference in granulation characteristics, it is required to reduce the resistance through the die hole in the process of granulation. For this reason, the die hole should be designed into two sections, feed extrusion section L and decompression discharge section R, namely L+R=T. There are three basic forms of decompression discharge hole: straight hole, cone hole and combination of cone hole and straight hole, among which the straight hole and cone hole are the most commonly used, its maximum aperture is slightly larger than the die hole diameter d, its depth depends on the corresponding effective working length L. In some cases, especially when the processing material appears in the deep pressure hole will expand and plug, it is appropriate to use the transition combination of cone hole and straight hole , or the use of cone hole.