Şirket Profili
Hangzhou Hanpai Kalıp Technology Co. Ltd. 2012 yılında kurulmuş olup, Zhejiang Kalıp ve Kalıp Endüstrisi Birliği'nin Konsey Üyesidir. Yem peletleri halka kalıbı, biyokütle peletleri halka kalıbı, organik gübre peletleri gibi pelet değirmeni makine parçalarının Ar-Ge ve üretiminde uzmanız. halka kalıp, kedi kumu peletleri halka kalıp, silindir kabuk vb.Dünya için sıfır kusurlu pelet değirmeni kalıbı sağlamak bizim geliştirme hedefimizdir.
2017 yılında Hangzhou yüksek teknoloji kuruluşu olarak onurlandırıldık ve Zhejiang eyaleti bilimsel ve teknolojik işletmelerinin onayını geçtik.2018 yılında şirketimizin adı Hangzhou Hanpai Mold Co., LTD'den Hangzhou Hanpai Mold Technology Co., LTD olarak değiştirildi. SGS tarafından Denetlenen Tedarikçiyiz, artık ISO 9001 kalite yönetim sistemi sertifikasına sahibiz.
Mutlu Kalıp, yüksek kaliteli X46Cr13 paslanmaz çelik, CNC derin delik delme makinesi, vakumlu söndürme fırını, diğer gelişmiş ekipman ve benzersiz süreci kullanır;Aynı zamanda, Happy Mold'un mükemmel kalitesini ve iyi müşteri itibarını yaratan bir grup üst düzey teknisyenimiz ve sıkı üretim kalite kontrol sistemimiz var. Happy Mold üretim verimliliğini %10-40 artırabilir, üretim maliyetini %10 azaltabilir -40%
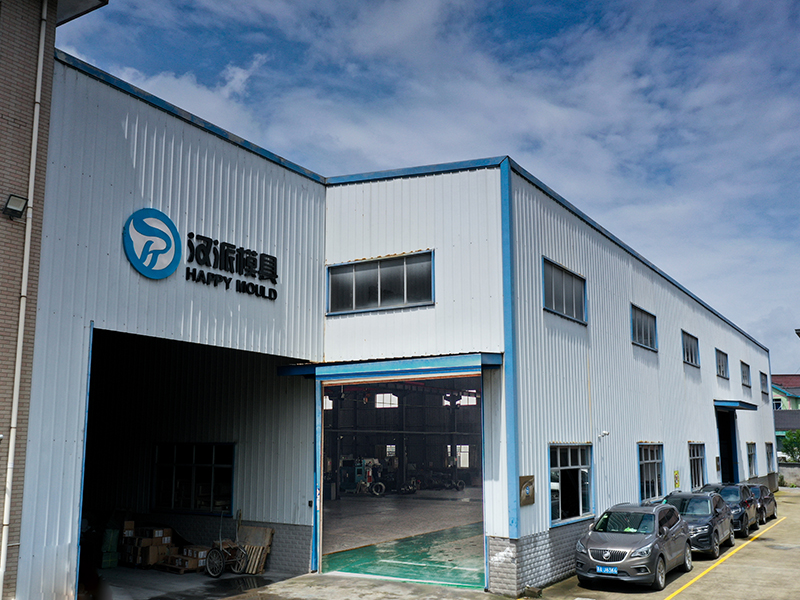
Mutlu Kalıp
"HAPPY MOULD" bizim ticari markamızdır; Happy Mold'un kullanılması, düzgün üretimi, iyi pelet kalitesi, yüksek üretim verimliliği, düşük güç tüketimi ve kolay kullanımı nedeniyle müşterinin çok fazla üretim maliyetinden tasarruf etmesini, karını ve pazar rekabet gücünü artırmasını sağlayabilir. İşçilerin emek yoğunluğunu azaltabilir, bu da herkese mutluluk getirir.
Hanpai Kalıp yurtiçi ve yurtdışındaki müşterilerden büyük övgü aldı ve küresel pelet üretim işletmeleri için mükemmel ve sıfır hatalı kalıp sağlamayı dört gözle bekliyoruz.
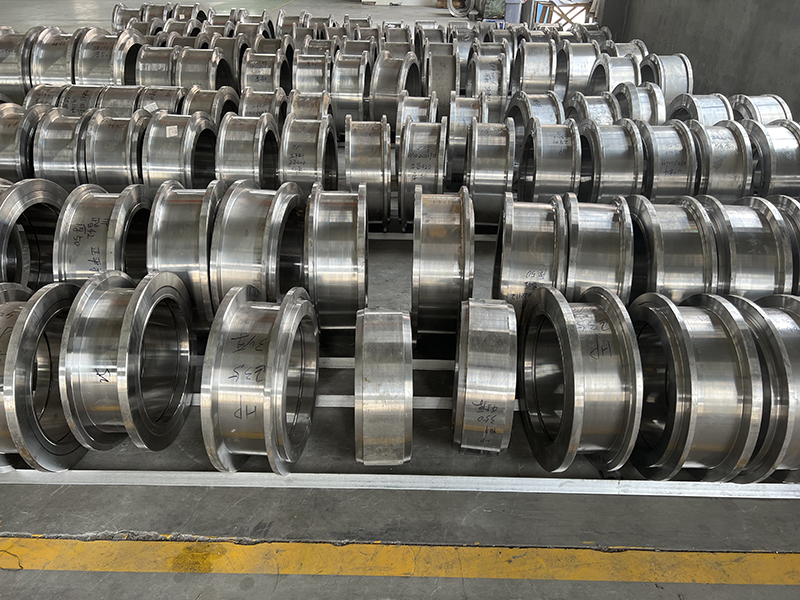
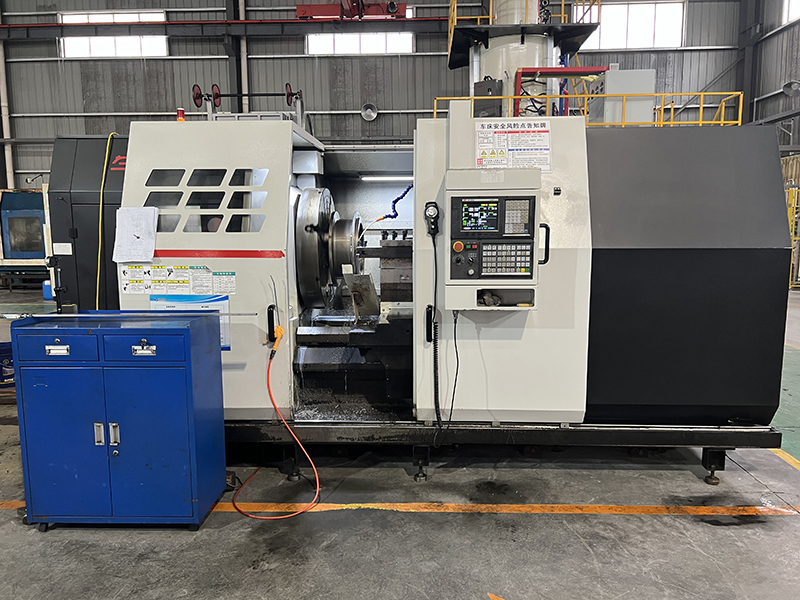
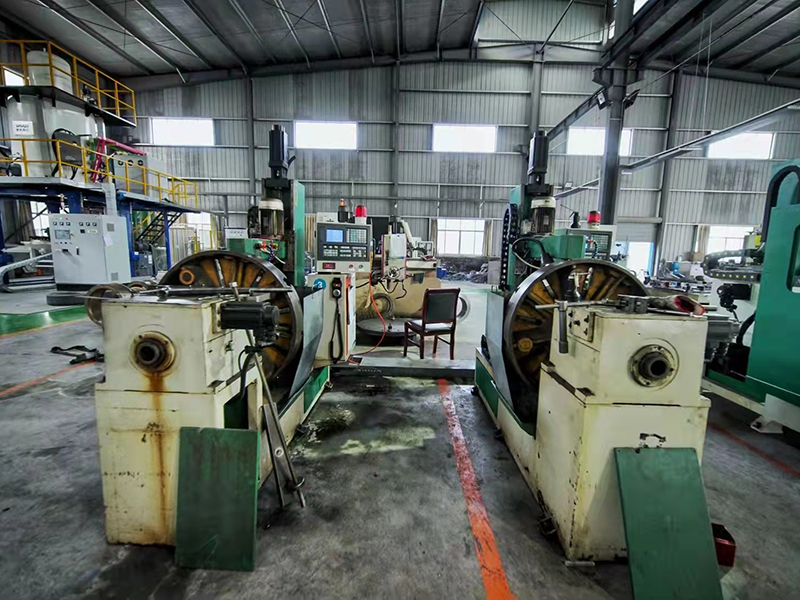
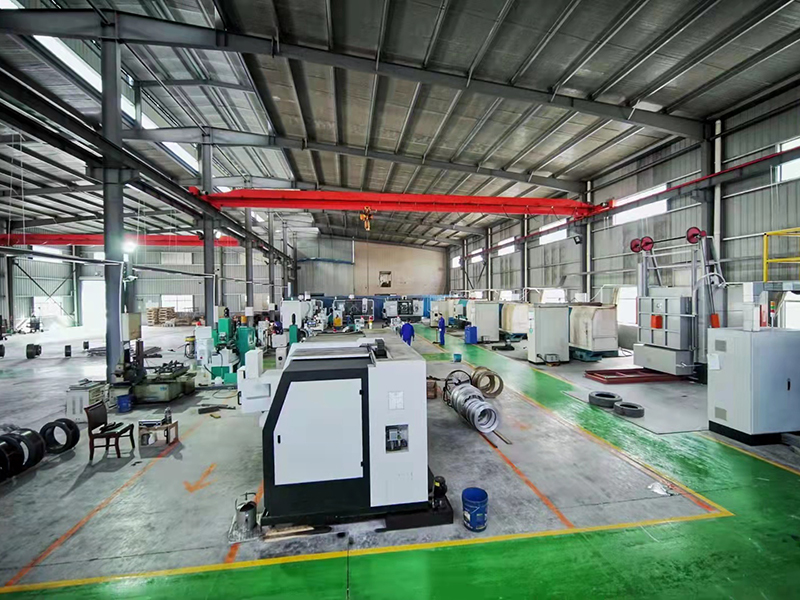
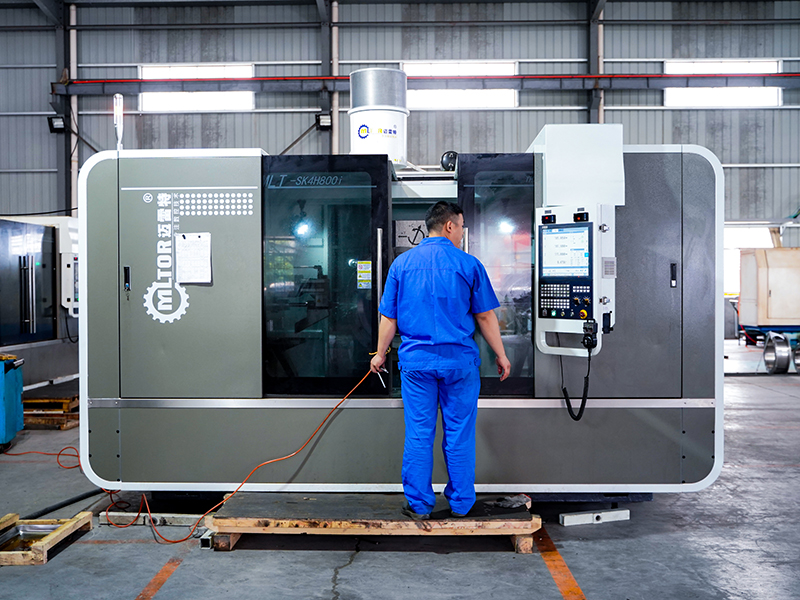
Şekildeki kimlik - halka kalıbının iç çapı;
O - halka kalıbının toplam genişliği;
W - halka kalıbının etkin genişliği (çalışma yüzeyi genişliği);
d - halka kalıbın açıklığı (preslenmiş peletin delik boyutu);
L - kalıp deliğinin etkin uzunluğu;
T - halka kalıbının toplam kalınlığı;
D - kalıp deliğinin konik giriş çapı;
β - kalıp deliği konik giriş açısı;
Pelet değirmeni kalıbının delik şekli: Yaygın olarak kullanılan delik şekilleri esas olarak düz delik, ters adım deliği, dış koni raybalama deliği ve konili ileri geçiş adımı deliğini içerir.Düz delik işleme basittir, en yaygın kullanımdır;Kalıp deliğinin etkin uzunluğu ve kalıp deliğindeki malzeme ekstrüzyon süresi, ters adım deliği ve dış konik delik tarafından azaltılır, çapı φ10 mm'den küçük olan peletlerin işlenmesi için uygundur.Konik şekilli pozitif raybalama adımı deliği, çapı φ10 mm'den fazla olan ve yüksek ham lif içeriğine sahip pelet beslemesinin işlenmesi için uygundur.Yukarıdaki 4 çeşit delik şekline ek olarak, dış konik delik, iç koni deliği ve dairesel olmayan delik gibi çeşitli delik şekilleri de vardır, ancak kullanımı yaygın değildir.
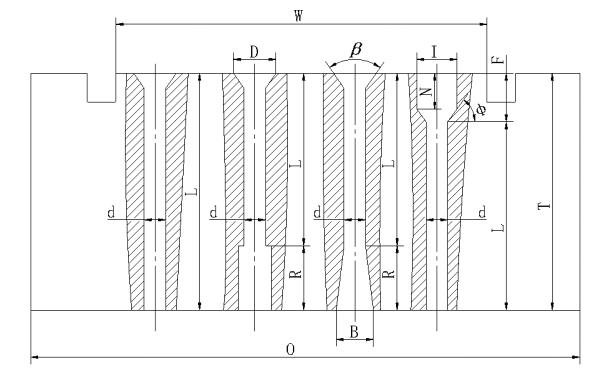
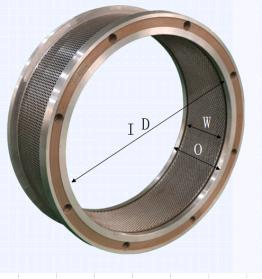
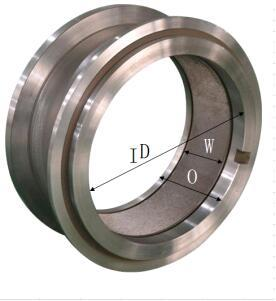
R - ters raybalama derinliği (basınç tahliye deliği);
B - ters raybalamanın çapı (basınç tahliye deliği);
φ -- pozitif raybalama geçiş açısı;
F -- pozitif raybalama derinliği;
I - pozitif raybalama çapı;
L/d -- uzunluk-açıklık oranı (sıkıştırma oranı).
Pelet değirmen kalıbının kalınlığı (T): Halka kalıbın kalınlığı, halka kalıbın mukavemetini, sertliğini ve peletleme verimliliğini ve kalitesini doğrudan etkiler.Dünyada, halka kalıbın kalınlığı (T) genellikle 32~127 mm arasında seçilir (Çin'de minimum kalınlık 13 mm'dir).
Pelet değirmeni kalıp deliğinin etkin uzunluğu (L): Halka kalıp deliğinin etkin uzunluğu, malzeme ekstrüzyonu (şekillendirme) için kalıp deliğinin uzunluğunu ifade eder.Kalıp deliğinin etkin uzunluğu ne kadar uzun olursa, malzemenin kalıp deliğindeki ekstrüzyon süresi o kadar uzun olur, peletler o kadar sert yapılır, bu durumda mukavemet ve pelet kalitesi daha iyi olur.Aksine peletler gevşek olur, tozlaşma oranı yüksek olur ve pelet kalitesi düşer.
Kalıp deliğinin konik giriş çapı (D): malzemenin deliğe direncini azaltmak ve girişini kolaylaştırmak için besleme deliğinin çapı kalıp deliğinin çapından (d) daha büyük olmalıdır. kalıp deliğine.Besleme deliklerinin düz delik, koni delik ve kavisli delik olmak üzere üç temel şekli vardır. Yüksek lif içeriğine sahip hammaddeler için, granülasyon özelliklerindeki farklılıktan dolayı, proseste kalıp deliği yoluyla direncin azaltılması gerekmektedir. granülasyon.Bu nedenle kalıp deliği iki bölüm halinde tasarlanmalıdır; besleme ekstrüzyon bölümü L ve dekompresyon boşaltma bölümü R, yani L+R=T.Dekompresyon boşaltma deliğinin üç temel biçimi vardır: düz delik, koni deliği ve koni deliği ile düz deliğin kombinasyonu; aralarında düz delik ve koni deliği en yaygın olarak kullanılır, maksimum açıklığı kalıp deliği çapından biraz daha büyüktür d derinliği karşılık gelen etkili çalışma uzunluğu L'ye bağlıdır. Bazı durumlarda, özellikle işleme malzemesi derin basınç deliğinde göründüğünde genişleyecek ve tıkanacak, koni deliği ve düz deliğin geçiş kombinasyonunun kullanılması veya kullanımın kullanılması uygundur. koni deliğinden.